Principle
Ultraviolet curing is a process in which UV energy produced by a mercury discharge lamp is absorbed by a sensitizer, causing a reaction in the monomer which makes it hard and dry. The rate of the curing process depends on the following:
1. Chemical compound - Each monomer cures at a different rate, depending on the amounts and compositions of sensitizer, pigment, and chemical additives.
2. Thickness of Coating - The thickness of a specific coating is not directly proportional to exposure time. The amount of
UV energy inside a layer of coating decreases exponentially with depth. If 70% of the
UV energy is absorbed in the top .001" of coating, then 70% of the remainder or 7% of the initial amount will be absorbed in the second .001" of coating. Thus, a two-fold increase in the thickness requires a ten-fold increase in
UV intensity.
3. Amount of UV per Unit Surface - Normally, the curing speed will increase with the amount of
UV energy per unit surface at the non-linear rate. If a 200 watt per inch mercury lamp was increased to 400 watt, the curing speed could increase ten fold. In additional, special metal halide lamps can trigger the receptor at an even faster rate with a standard 200 watt per inch lamp. The chart on Figure 1 demonstrates the flexible control of Innovative's lamps. We can pinpoint the
UV energy produced by our curing lamps to your exact specifications.
The sensitizer should absorb UV in the range which is not absorbed by the monomer or pigment. The wavelength produced by a medium pressure mercury lamp or metal halide lamp should coincide with the wavelength absorbed by the
sensitizer.
|
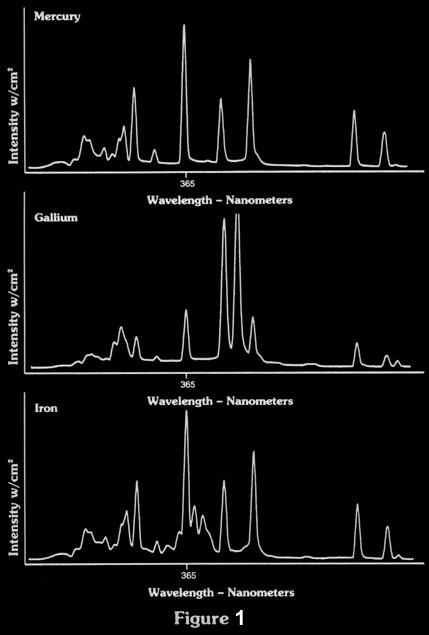 |
UV
Curing
The types of radiation emitted from our mercury lamps depend on many factors. In a gas discharge lamp, the output is a function of the atomic structure of the gas molecules, their temperature, and the pressure of the gas vapor.
If you require the absence of ozone gases, our engineering department can respond with a special grade of quartz that prevents the 25 nanometer line from reaching oxygen in the atmosphere. Please bear in mind that all effective lines below 254 nanometers are blocked, which may interfere with the curing of some inks. Figure 2 shows the basic area of interest for industrial curing.
The UV Spectrum
The far ultraviolet lies between 200 nm and 300 nm and is classified as Germicidal or
UV-C. The middle ultraviolet lies between 280 nm and 320 nm is called Erythema (suntan) or
UV-B. The near ultraviolet lies between the 320nm and 400nm and is commonly called Black Light (long ultraviolet) or
UV-A.
Innovative Machine's medium pressure lamps builds vapor pressure as the power and temperature start to increase. As shown in the table below, as the power input increases, so does the efficiency (ratio of total radiation to power input. From 100 watt per inch to 3000 watt per inch the efficiency is increased by 12%)
|
Input Power (watt/inch)
|
Efficiency R/P %
|
|
40 |
27 |
|
50 |
36 |
|
100 |
54 |
|
200 |
63 |
|
300 |
66 |
|
400 |
67.5 |
Total Radiation Efficiency
Our 400 watt per inch lamps will more than double the cure when compared to two lamps running 2000 watt per inch. The spectral charts in Figure 5 give a comparison of the ultraviolet output of the voltage lamp operated at 200, 300, 400,and 500 watt per inch by varying the secondary current applies to the lamp.
The spectral output does not shift as the lamp power is increased from 100 to 200 to 300 watts per inch. There are a multitude of medium pressure mercury lamps varying in shape, size, diameter, length and power output. Please note that an Innovative Machines lamp operating on a properly designed stabilized ballast has a power conversion from line input to lamp output of 92%.
Technical nformation
provided by the manual 'Superior Quartz Products,' which is property of
Superior Quartz, Inc.
|